生産ラインにおける投入順序最適化
概要
生産ラインにおいて、投入順序は生産効率に大きく影響します。そのため、「最適な投入順序を導き出す」ことは生産現場において重要な課題です。スケジューラの使用や、少ない投入種類数であれば机上計算で最適解を導出できるかもしれませんが、想定する状況が複雑化したり、投入品の種類の数が多くなると、スケジューラや机上計算では最適な解を見つけることが困難です。
そこで、WITNESSと最適化オプションのExperimenterを使って、自動的に最適に準ずる投入順序を作成した事例をご紹介します。
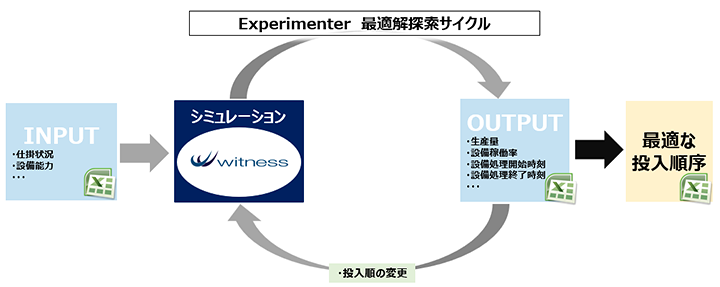
上図に示す概念図のように、WITNESSでモデルを作成し、出力値を評価し、投入順序を変更しながら繰り返しシミュレーションを実行することで、より良い解を探索し、最適な投入順序にアプローチしていきます。
WITNESSを使うことによって、生産ライン上での製品の滞留といった待ち行列要素や、マシンや作業員などの取り合いを考慮できるため、スケジューラでは考慮できない事象の影響も解析しながら最適化の解を探索することができます。
生産ラインにおける投入順序最適化の事例
本事例では、投入パーツ種類数が100種類を超える生産ラインに対して、人の手で最適と思われる順序に設定したベンチマークモデルを作成し、最適化計算の結果と比較検討を行いました。
このモデルでは100の階乗以上の膨大な組み合わせについて最適解を求めるため、SA法(Simulated Annealing)を用いて最適化を行っています。目的関数は、「すべての生産品の生産が終了するのにかかった時間」と定義しています。
この方法を使用した場合、24時間以内の解析時間で、ベンチマークモデルよりも「1稼働日当たり数十分、生産処理が早く終了する」という結果を得ることができました。
以下のキャプチャはExperimenterの最適化実行画面の一例です。結果を簡単にソートすることができるので、最適な投入順序を把握するだけでなく、目的関数以外の指標を定義しておくことで、多角的な分析をすることも可能です。
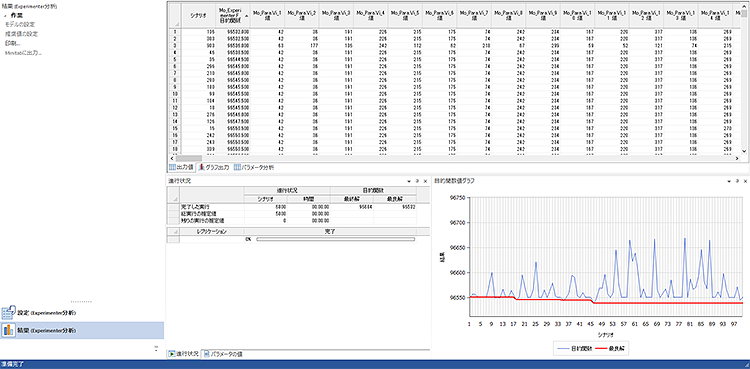