カート式配送センター
WITNESSを用いた物流システムのモデリングの1例を紹介します。日用品大手メーカーA社様向けに開発された大規模・詳細な庫内物流モデルを、A社様のご協力でご提供いただき、簡略化した上でご紹介しています。
モデルの目的
WITNESSを用いた物流システムのモデリングの1例をご紹介します。ここでは、日用品大手メーカーA社様向けに開発された大規模・詳細な庫内物流モデルを、A社様のご協力でご提供いただき、簡略化した上でご紹介しています。
庫内物流の基本的な単位には、梱<こり>(ダンボール箱など、商品が1ダースなどのまとまった数量で梱包された荷姿)とバラ(梱をバラして、商品一つひとつにした荷姿)があります。日用品の流通を単品管理するためにはバラ荷への対応が必要になります。つまり、「今日は品番○○を5箱と7本出荷する。」というような考え方が必要になるわけです。
A社様ではきわめて多品種の日用品を製造されており、商品構成も新商品開発や季節変動によりつねに変化しています。他方、配送先はそれほど多くないため、カート台車式の配送センターを検討されました。
このような、カート台車式バラピッキング配送センターの能力の検証が、このモデルの目的です。
問題
カート台車式バラピッキング配送センターの能力検証が難しいのは、まず第1の要因として、考慮すべきパラメータが非常に多いことが挙げられます。例えばA社様の事例では
- 作業者の人数
- カート台車を運転しながらピッキングなどの作業を行う作業者の人数。
- 間口のレイアウト
- 配送先に対応する各間口のレイアウト。
- 作業所要時間
- 作業員が、カート台車への積み込みやピッキングを行うのに必要な所要時間、折りコンテナの組立所要時間、バーコード等のスキャンに必要な時間等。
- カート台車に積載可能な商品の数量
- これは、各商品固有の体積や底面積などにより変動します。
このようなさまざまなパラメータをすべて考慮する必要があります。第2の要因として、カート台車式ではコンベア式に比べてフレキシブルな対応が可能である一方、作業員人数(カート台車台数)が増えれば増えるほど複雑な相互干渉を引き起こすことが挙げられます。具体的には以下のような問題を考慮しなければなりません
- 作業者の待ち方が複雑
- カート台車が間口より大きいため、1台のカート台車が3列程度の間口をふさいでしまいます。そこで、ふさがれた間口に商品を置きたい作業者は、「横で待つか、後ろで待つか?」といったような「待ち方」を考える必要があります。
- 追い越し可能
- 一般的なコンベアと違ってカート台車式では、作業者は、商品を置きたい間口が遠くにある場合には前を進む作業中の作業者を追い越して行くことができます。また、追い越した先の間口が更に別のカート台車によってふさがっていないかといったような要因も考慮する必要があります。
モデルの概要
このモデルで扱われている配送センターは、下図のようなレイアウトになっています。
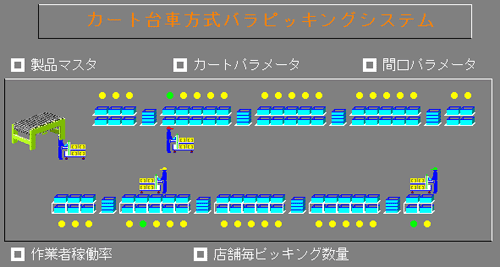
カート台車式バラピッキング配送センターのモデル
実際の現場と比べると簡略化されたモデルですが、カート大蛇方式のバラピッキングを行う配送センターの主要な用件を検討できます。作業員は、「カード台車の概略ルート」に従って右回りに周回します。ただし必ずしも右端まで行く必要はなく、目的の間口が現在の位置よりも右側に無い場合には、下側のゾーンに移動します。WITNESSを使用する事で作業員のフレキシブルな行動のモデル化を行う事ができます。
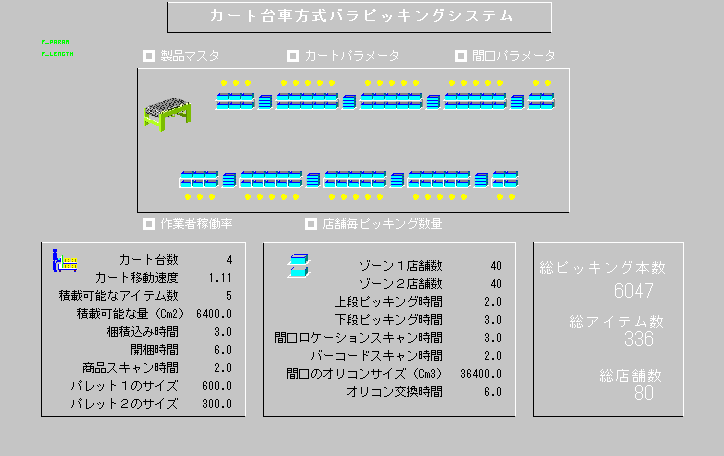
おおよそ25分間に相当するシミュレーションです。ムービーが2/3ほど進んだところで、先頭を走るカート台車を2番目のカート台車が追い越して行きます。
各間口の丸いインジケーターは、各間口の状態を表しています。
- ● アイドル状態
- ● カート台車から間口への積み込み作業中
- ● 他のカート台車に邪魔されて目的の間口に行けないカート台車が停車中
配送センターでの作業の流れは、以下のようになっています
- カート台車への積み込み
- 画像左端に配置されているコンベアで、梱単位の商品が運ばれてきます。これをカート台車に積み込み、各間口(40ヶ所)に作業員が仕訳してゆくわけです。作業員が混乱しないように、カート台車積載可能な商品の種類は5種類までとしています。また最大積載量は、各商品の梱固有の底面積、端数用パレットの底面積、およびカート台車の積載面積から決まり、一定積載量以上は積むことができません。
- 作業員の運搬・仕訳け
- 間口は2段に配置され、折りコン1個がそれぞれ1出荷先(小売店舗)に相当します。作業員は時計周りに周回し、商品を指定の間口に投入してゆきます。運搬作業の間に、必要なバーコードをスキャンしたり、折りコンが一杯になった場合にはその折りコンの「押し出し」(出荷)および新しい空の折りコンの組み立てを行います。
たくさんのモデルパラメータのうち主な項目と、上に示したシミュレーション画面での設定状況は下表のようになっています。これらを変更していろいろなパターンのシミュレーションを簡単に実施することができます。
カート台車関係のパラメータ
カート台車数 | 4 | (台) |
---|---|---|
カート台車移動速度 | 1.11 | (m/sec.) |
積載可能なアイテム数 | 5 | (種類) |
積載可能な量 | 6,400 | (cm2) |
梱積み込み所要時間 | 3.0 | (sec.) |
開梱時間 | 6.0 | (sec.) |
商品バーコードスキャン時間 | 2.0 | (sec.) |
パレット(大)のサイズ | 600 | (cm2) |
パレット(小)のサイズ | 300 | (cm2) |
間口関係のパラメータ
間口数(ゾーン1) | 40 | (ヶ所) |
---|---|---|
間口数(ゾーン2) | 40 | (ヶ所) |
上段ピッキング時間 | 2.0 | (sec.) |
下段ピッキング時間 | 3.0 | (sec.) |
間口ロケーションバーコードスキャン時間 | 3.0 | (sec.) |
間口バーコードスキャン時間 | 2.0 | (sec.) |
折りコンテナ交換時間 | 6.0 | (sec.) |
入力データ
配送センターに対し、商品の発注データを次のような入力ファイルで与えます。
モデルの入力データ
日付 | 品番 | 出荷先コード | 出荷数量 | 入数(個数/梱) | 1梱の底面積 | 1梱の体積 |
---|---|---|---|---|---|---|
xxxx0514 | 1 | 4 | 6 | 12 | 1000 | 64000 |
xxxx0514 | 1 | 38 | 6 | 12 | 1000 | 64000 |
xxxx0514 | 1 | 50 | 6 | 12 | 1000 | 64000 |
xxxx0514 | 1 | 59 | 3 | 12 | 1000 | 64000 |
xxxx0514 | 1 | 69 | 6 | 12 | 1000 | 64000 |
xxxx0514 | 2 | 3 | 3 | 24 | 1000 | 64000 |
xxxx0514 | 2 | 14 | 3 | 24 | 1000 | 64000 |
xxxx0514 | 2 | 39 | 6 | 24 | 1000 | 64000 |
xxxx0514 | 2 | 50 | 3 | 24 | 1000 | 64000 |
xxxx0514 | 2 | 76 | 3 | 24 | 1000 | 64000 |
xxxx0514 | 3 | 58 | 3 | 48 | 1000 | 64000 |
xxxx0514 | 4 | 12 | 3 | 48 | 1000 | 64000 |
xxxx0514 | 4 | 39 | 2 | 48 | 1000 | 64000 |
xxxx0514 | 4 | 58 | 3 | 48 | 1000 | 64000 |
このモデルではCSV(カンマ区切りテキスト)ファイルを入力データとしています。WITNESSはこの入力ファイルを読み込み、製品別に集計し、梱数・作業に投入する荷姿(梱 and/or バラ)・作業順序(どの品番から作業するか)を決定します。作業順序の決め方にはいくつか考えられるのですが、例えば総数の多い順に作業をする場合、ピッキング作業に投入する商品のデータ(ピッキングリスト)は次のようになります。
作業順序を考慮したピッキングリスト
品番 | 出荷数量 | 形状 | 必要面積cm^2 |
---|---|---|---|
60 | 96 | 4 | 1000 |
60 | 54 | 2 | 600 |
186 | 30 | 4 | 1000 |
186 | 30 | 4 | 1000 |
186 | 30 | 4 | 1000 |
186 | 30 | 4 | 1000 |
186 | 16 | 2 | 600 |
224 | 120 | 4 | 1000 |
224 | 12 | 1 | 300 |
15 | 20 | 4 | 1000 |
15 | 20 | 4 | 1000 |
15 | 20 | 4 | 1000 |
15 | 20 | 4 | 1000 |
15 | 20 | 4 | 1000 |
形状番号 | 説明 |
---|---|
1 | 半数以下 |
2 | 半数以上 |
4 | 全数 |
出力データ
このモデルで生成されるレポートをいくつか示します。これらはいずれもMicrosoft Excelのワークシートに直接出力していますので、レポートの加工やグラフ化も容易に行うことができます。
すべてのピッキングリストのすべての商品(6,047個)をピッキングするのにかかった所要時間は、10,782秒(約180分)です。
ピッキング所要時間についてのレポート
日付 | 総数 | ピッキング所要時間 |
---|---|---|
xxxx0514 | 6047 | 10782.3 |
このモデルは、作業者の分析に主眼をおいており、作業者については詳細なレポートを出力しています。
作業者についての詳細なレポート
作業状況出力
作業者No | 周回No | ケース数 | 個数合計 | 品番 | 数量 | 時間 | |||||||||||||
---|---|---|---|---|---|---|---|---|---|---|---|---|---|---|---|---|---|---|---|
品目1 | 品目2 | 品目3 | 品目4 | 品目5 | 品目1 | 品目2 | 品目3 | 品目4 | 品目5 | 積み込み待ち | 積み込み | ピッキング | 実車移動 | 空車移動 | 待ち | ||||
2 | 1 | 7 | 232 | 224 | 15 | 0 | 0 | 0 | 132 | 100 | 0 | 0 | 0 | 67 | 67 | 884 | 52 | 10 | 290 |
1 | 1 | 7 | 286 | 60 | 186 | 0 | 0 | 0 | 150 | 136 | 0 | 0 | 0 | 0 | 67 | 1148 | 87 | 3 | 190 |
3 | 1 | 7 | 201 | 15 | 213 | 247 | 0 | 0 | 18 | 111 | 72 | 0 | 0 | 134 | 69 | 731 | 65 | 5 | 619 |
4 | 1 | 7 | 366 | 247 | 225 | 35 | 88 | 226 | 27 | 96 | 85 | 80 | 78 | 203 | 73 | 1273 | 73 | 3 | 669 |
2 | 2 | 7 | 352 | 223 | 120 | 131 | 198 | 324 | 75 | 70 | 69 | 69 | 69 | 0 | 73 | 1308 | 79 | 3 | 0 |
1 | 2 | 7 | 156 | 211 | 334 | 241 | 0 | 0 | 66 | 63 | 27 | 0 | 0 | 0 | 69 | 614 | 68 | 4 | 686 |
3 | 2 | 7 | 93 | 241 | 275 | 0 | 0 | 0 | 33 | 60 | 0 | 0 | 0 | 0 | 67 | 342 | 55 | 3 | 903 |
4 | 2 | 7 | 170 | 194 | 102 | 11 | 0 | 0 | 59 | 57 | 54 | 0 | 0 | 0 | 69 | 601 | 68 | 5 | 55 |
2 | 3 | 7 | 175 | 333 | 36 | 17 | 255 | 0 | 54 | 49 | 48 | 24 | 0 | 0 | 71 | 690 | 64 | 5 | 0 |
1 | 3 | 7 | 140 | 255 | 13 | 42 | 57 | 0 | 24 | 47 | 45 | 24 | 0 | 0 | 71 | 501 | 66 | 3 | 224 |
3 | 3 | 7 | 89 | 57 | 237 | 7 | 0 | 0 | 21 | 44 | 23 | 0 | 0 | 0 | 69 | 395 | 75 | 3 | 293 |
4 | 3 | 8 | 187 | 7 | 61 | 87 | 202 | 228 | 19 | 42 | 42 | 42 | 42 | 0 | 82 | 680 | 72 | 3 | 219 |
2 | 4 | 7 | 199 | 305 | 9 | 33 | 58 | 89 | 42 | 40 | 39 | 39 | 39 | 0 | 73 | 774 | 75 | 3 | 0 |
1 | 4 | 7 | 102 | 182 | 188 | 332 | 0 | 0 | 39 | 39 | 24 | 0 | 0 | 0 | 69 | 406 | 60 | 3 | 260 |
各行は、作業者別・周回別となっています。非常に長いレポートなので、第1周回から第2周回までのレポートのみを掲載しています。
各作業者は5種類までの品目を扱うことができます。例えば2番の作業者(表中赤字で記載)は、第1周回では2種類の品番の商品を、第2周回では5種類の品番の商品を扱っています。なお、第1周回で2番の作業者が1番の作業者を追い越しているため、作業者No.は2→1→3→4の順になっています。
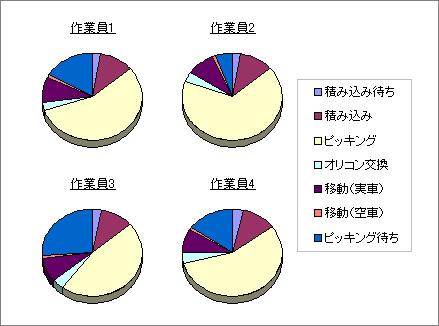
作業者の各作業についての詳細なレポート
結果および評価
モデル内のカート台車の台数(作業者の人数)を1台から5台まで変化させてシミュレーションを実施し、生産性がどの程度変化するのかを検討したケーススタディーの結果以下に示します。
カート台数による生産性の変化のシミュレーション結果
カート台車台数 | 所要時間 | 1秒あたり処理個数 | 1台の場合に 対する比率 |
---|---|---|---|
A | B | C=6047/B | |
(台) | (秒) | (個/秒) | |
1 | 34845 | 0.17 | 1.00 |
2 | 18014 | 0.34 | 1.93 |
3 | 12696 | 0.48 | 2.74 |
4 | 10782 | 0.56 | 3.23 |
5 | 8829 | 0.68 | 3.95 |
カート台数を1台から5台まで1台づつ増加させると所要時間は短縮し生産性も増加しますが、その増加の度合いは徐々に小さくなる結果になります。これは限界生産性逓減則そのものです。しかし台数を増やすと逆に生産性が低下するまでには至っておらず、カート台車5台までであれば、例えば繁忙期にカート台車と臨時雇いの作業者を増やすことにより納期(所要時間)を守ることが可能であることがこのケーススタディーから確認できます。
「NCドリル工場」や「自動車工場艤装工程」のモデルでは多額の投資をした設備の生産性や、そもそもラインが成立するかどうかが重要な検討項目でした。しかしAGVやコンベアに比べてカート台車は安価であり、むしろ変動する需要や商品構成に応じて納期(所要時間)を守り、多品種少量の複雑な流通を回してゆけるかどうかがカート台車式配送センターの主要検討項目となります。フレキシブルな動作をする作業者(カート台車)や梱・バラの流れを詳細にモデル化可能なWITNESSを使用する事によって、様々なケースを検討する事ができます。