富士重工業株式会社 様「AdvantEdge」による切削シミュレーションで
部品製造加工の大幅な効率化を実現

お話を伺った方
群馬製作所 大泉工場 製造品質管理部 P/U開発主査
上井 智聡様
富士重工業株式会社(以下、富士重工)は1917年に創業の中島飛行機を前身に、1953年に創立された。1958年には「スバル360」を発売、我が国のマイカーブームの先駆けとなったことはよく知られている。現在は「SUBARU」ブランドで親しまれている自動車製造部門と戦前から引き継いだ航空機製造部門および産業機器部門等がある。自動車を製造する群馬製作所(スバル自動車部門)は、群馬県太田市の本工場、矢島工場、太田北工場、大泉工場および伊勢崎工場があり、エンジンから最終の車両組み立てまでを一貫して行っている。また、大泉工場で生産されたエンジンは、国内のみならずアメリカの同社工場に供給している。群馬製作所はまさに富士重工の一大生産拠点となっている。一方、航空機製造部門は栃木県と愛知県で航空機・宇宙関連機器とその部品を製造する他、風力発電機、お掃除ロボット、産業機器部門では草刈機、発電機などを製造、販売している。このように富士重工は、日本を代表する重工メーカーである。
いま、自動車業界ではCO2低減など環境車への対応や製造コストの低減が大きなテーマとなっています。燃費改善のため自動車を軽くすることや、安全性を確保しながら製造コストを低減するには、部品一つひとつにまで細かな配慮が求められます。富士重工では、トランスミッションに使用される部材の加工方法を、CTCが販売する2次元/3次元切削専用有限要素法プログラム「AdvantEdge」でシミュレーションし、従来の研磨から切削に加工方法を変えることで大幅な効率アップを実現しました。
インタビューでは斬新な加工方法を考案したいきさつや「AdvantEdge」を使ったシミュレーションの活用事例とその効果などについて伺いました。
スバルのエンジン、トランスミッションを生産する大泉工場
大泉工場は、エンジンとトランスミッションの加工、組み立て、生産を一貫して行い、国内はじめアメリカの工場へ供給しています。ここで製造されるエンジンは、軽自動車用660ccエンジンから小型車用1.5リットルから3.6リットルまでの水平対向エンジンとターボエンジン、2リットルのディーゼルエンジンなどがあります。トランスミッションは、軽自動車用CVT、小型車用では4AT、5AT、そして新しく開発したチェーン式CVTなどがあります。
水平対向エンジンは長年にわたるノウハウを活かし、高剛性、コンパクトなことに特徴があります。ディーゼルエンジンは、燃焼時の圧縮比が高いことからエンジンまわりの強度が求められるため、主に大型車に使用されていましたが、当社ではガソリン車と変わらない大きさを実現、普通乗用車のディーゼル車普及に弾みをつけました。
私が所属する製造品質管理部は、お客様に喜ばれる商品を目指し品質向上を図るべく、問題が生じた際の原因究明と対策を講じる他、過去の経験で得られたノウハウを生産車や開発中の車へ活かし常に改善を図っています。また、エンジンやトランスミッションなどのユニットから完成車両に至るまで最終的なチェックを行うなど、業務は多岐にわたります。
自動車は多種多様な部品から構成されているため、自社製品のみならずサプライヤーの製品に対しても自社製造製品と同様に、迅速に対応できる体制を整えています。サプライヤーを含め部品モジュールの共通化が進むに伴い、問題の早期発見と素早い対応は、重大な障害を未然に防ぐことに最も重要です。
燃費がよくかつ安全性に配慮したクルマを目指す
自動車業界では、ハイブリッド車や電気自動車などエコカーに注目が集まっています。当社も2009年7月から官公庁や電力会社などの法人向けに電気自動車の販売を開始しました。
このように環境へ配慮した自動車を生産する一方、いま一番重要なテーマは燃費の改善です。富士重工は、ドライバーズカーとして「安全性、操縦安定性のよいクルマづくり」を行ってきました。ある面では燃費の改善と相反する所がありますが、この問題を解決するために安全性を損なわずに燃費をいかに良くするかが大きなテーマとなっています。その1つに、エンジンやトランスミッションの改良が挙げられます。軽量化である部材の薄肉化、トランスミッションの小型化・高機能化は燃費改善に大きな効果があります。
トランスミッションの小型化・高機能化も当社ならではの技術力によって、斬新なシステムを採用することで燃費の改善に成功しました。
トランスミッションはCVT(Continuously Variable Transmission=無段変速機)が主流となりつつあります。その理由は、燃費改善にはエンジンの燃焼効率のよい領域を常に使うように制御し無駄なくタイヤに動力を伝えることが必要だからです。CVTは一般的には金属ベルト方式を採用していますが、ベルト方式ではある変速比を確保しようとするとそのためのスペースが必要になります。スペースが必要ということは、それだけサイズも大きくなり、燃費の面で問題があります。そこで考案したのがベルトの代わりにチェーンを用いることでした。チェーン式にすることでコンパクト化し、かつトルク伝達の効率も向上させたトランスミッションを開発したことで、大幅な燃費向上を実現しました。新しいレガシーにはチェーン式のCVTが採用されています。
「AdvantEdge」によるシミュレーションで画期的な部材加工法を開発
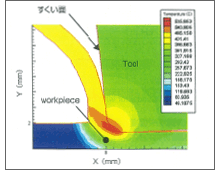
自動車メーカーにとってもう1つの大きな課題は、「いいクルマを低コストで生産すること」です。部材の加工方法を変えることで、生産性は大きく変わります。当社は、工具コストを毎年10数%低減することを目標としています。しかし、自動車の部品、部材はクルマの性能や安全性に関わるため、加工方法を変えることは容易ではありません。そうした状況の中で取り組んだのが、CVTに使われる部材の加工法の改善です。
CVTのプーリーという部品では、ボールスライド機構があります。その部品を熱処理したあとに、ボールが入る溝(以下ボール溝)を一溝ずつ小さな砥石で研磨して仕上げていました。しかし研磨では1個仕上げるのに約3分かかっていましたので、研磨ではなくブローチによる切削加工で、簡単に、早く、安価にできないかということを考えました。当時は生産技術を担当しており、その設備が高価で老朽化も進んでいたことから違った工法の必要性を感じていたのと、その時、ある方から中小企業の工場では手直しとしてハイス工具で熱処理後の硬い部材を加工しているという話を聞いて、トランスミッションの部材の加工に使えるのではないかと思ったことがきっかけです。ただし、求められる精度はミクロン単位。部材もHRC60というヤスリも歯が立たない非常に硬い素材で、一般にはCBN工具やセラミックなどの工具で切削加工するものですが、ブローチ工具にすると非常に高価となりとてもコストが見合わない。よってブローチ工具には超硬を採用することで決めました。一般的に工具硬度は材料の5倍程度必要と言われていますが、HRC60に対して超硬は2.5倍程度しかなく、試験的に加工したら3個で欠けてしまい、その時は途方にくれました。
そこで何かいい方法がないか探していたところ、切削専用のシミュレーションソフトウェア「AdvantEdge」があることを知りました。AdvantEdgeの機能を見ると、面白そうなソフトウェアでした。さっそくテストとして多くの条件を変えて試したところ“これは使えそうだ”ということが分かり、2002年に導入しました。
AdvantEdgeに求めた機能はシミュレーション結果の精密さより、限られた開発期間で、どの材料を使い、どういう加工条件が最適かをシミュレーションによって明らかにすることでした。早く決断するために、切刃に発生している現象を誰の目でも見えて対策を講じることができるツールが欲しかったからです。
AdvantEdgeでは、加工条件である切り込み量、切削速度のパターンを変えて切刃に発生している切削温度や応力などをシミュレーションし、実験結果と突き合せました。その時の工具磨耗状態とシミュレーション結果に基づく切削温度等から必要な工具設計仕様を工具材料メーカーに問い合わせしました。そして工具材料である超硬材の添加物、粒子の径、コバルト量などを決定し、結局専用の特注材料になってしまいましたが、工具材料メーカーさんも快く引き受けてくれました。同時に、コーティングとその使用方法についてもシミュレーションしました。このときは耐熱、耐磨耗性にすぐれたチタンアルミナ系を採用していましたが、切削すると逃げ面側のコーティング層が剥離する問題が発生しました。シミュレーション上でも実際と同様の個所に大きな圧縮応力が発生していたことから、圧縮割れと推測。そこで通常は強度アップのためコーティングを厚くするのに対し、逆に薄くすることで解決しました。こうしたシミュレーション結果を基に素材に使用する材料と工具の仕様を決め、その仕様に基づいて実証実験を行った結果、当初の予想通りの結果が得られました。それからは開発スピードが上がり、何とか量産化の日程には間に合いました。今考えると、工具も1本あたり百万円以上もするのでシミュレーションがなかったらいくら開発費用がかかったのだろうとぞっとします。
研磨加工から切削加工への変更で大幅な効率アップを実現
このようにAdvantEdgeは、部材の選定から新しい加工法の検討と工具の開発、工具の管理までさまざまに活用しました。
研磨加工から切削加工に切り替えた結果、次のような効果がありました。
- 研摩に比べ刃物にかかるコストを20%低減
- 加工時間が3分から15秒(実際の切削時間は1秒)へと大幅にスピードアップ、設備費が7分の1に
- 電力を約80%削減
- 油を使用しない
- スペースを90%削減
以上のような効果に加え、シミュレーション手法を用いることで客観的に数値を示すことが可能となり、刃物メーカーや工具メーカーに具体的な要求仕様を提示できるようになりました。工具開発は、工具メーカーとの共同研究で行っていましたが、シミュレーションによって数値を示せるようになった結果、こちら側の提示した仕様に納得して開発いただけるという効果がありました。
社内にシミュレーション技法を根付かせたAdvantEdge
AdvantEdgeは、現在は製造部門の現場での改善に役立てています。製造部門は毎年工具のコストダウンが要求されており工具の改良が行われています。しかし、現場の経験者がいいと判断して改良しても、実際とは異なってしまうことが多々あります。そういうときに、シミュレーションにより定量的に数値を把握することは、改善をスムーズに進める上で非常に有効です。もちろん、シミュレーション結果がすべてではありません。シミュレーション結果の善し悪しを最終的に判断するのは人間です。判断をするためにはシミュレーションと現物を突き合わせていく知識・経験の積み重ねが必要です。そういう面からも、シミュレーションはひとつの人材育成のツールといってよいでしょう。これからも現場でAdvantEdgeを利用し、シミュレーション技法を根付かせていきたいと思います。
AdvantEdgeは材料モデルも豊富になり、使い勝手も進歩しました。今後は、加工後の精度を予測する連成解析など、最終評価までシミュレーションできるようになることを期待しています。
サポートも万全で安心して導入できるCTCのソフトウェア
CTCとの出会いは、トランスミッションの部材の加工から始まりました。AdvantEdgeの導入に際しては、お互いのレベル合わせが必要なことからどの程度サポートしていただけるかが一番の気がかりでしたが、納得するまで十分なサポートをしていただけて満足しています。さらに、シミュレーションを行うことで知識の向上が図られるとともに定量的な見方が身に付き、現場から上がってきた要望をきちんと捉え、答えることができるようになったことも成果の一つです。このようにAdvantEdge を導入したことが、工具開発から現場の生産性改善、個々のスキル向上など当初の予想を超える効果がありました。
今後ともCTCと連携し、さらなる改善を進めていきたいと思っています。
富士重工業様は、AdvantEdgeの古くからのユーザーです。開発元とともにAdvantEdgeを進化させていく上でも貴重なご意見をいただいており、大変お世話になっております。
AdvantEdgeはシミュレーションに慣れていない方でも簡単に利用することができるソフトウェアですが、現場で現実的に利用できるツールとして浸透させていく過程をお客様の視点からお話いただき、大変勉強になりました。
さらなるコスト削減に繋がるよう、微力ながら協力させていただければと考えています。
長時間にわたるインタビューをご快諾いただき、誠にありがとうございました。
(聞き手:CTC宮口、押尾)
名称 | 富士重工業株式会社 (英訳名:Fuji Heavy Industries Ltd.).) |
---|---|
本社所在地 | 東京都新宿区西新宿一丁目7番2号 |
代表者 | 代表取締役社長 森 郁夫 |
設 立 | 1953年(昭和28年)7月15日 (創業:1917年(大正6年)5月) |
資本金 | 153,795 百万円 |
社員数 | 12,801人 (連結会社 合計25,598人) |
事業内容 | 【自動車】軽自動車、小型自動車、普通自動車ならびにその部品の製造、修理および販売 【航空宇宙】航空機、宇宙関連機器ならびにその部品の製造、販売および修理 【産業機器】発動機および発動機搭載機器、農業機械、林業機械、建設機械その他各種機械機具ならびにその部品の製造、修理および販売 【エコテクノロジー】特殊車両、塵芥収集車等の製造、販売および修理 |
(富士重工業様Webサイトより引用) ※2008年3月現在 |